LARGE FOOTPRINT FORM, FILL AND SEAL MACHINE (FFS)
A large medical device manufacturer attempted to transfer the packaging process for an extra large endoscopy device from a manual tray sealer to a large footprint FFS machine, which produced a 19.5 in by 10 in PETG tray, 45 mil thickness. The tray design was not adequate, and the customer had to implement foam pads in the folding cartons and an extra large corrugate shipper box with large 3 inch corrugate spacers in two sides of the shipper box in order to pass ASTM D4169 transportation testing. The added packaging components and padding made the cost of the packaging system too expensive and the packaging process inefficient. Pucará Engineering was called to redesign the entire packaging system. We used the raw material’s mechanical properties to our advantage, and added geometrical features within the design of the PETG tray intended to absorb the kinetic energy observed during shock and vibration when testing the product per ASTM D4169. The new PETG tray redesign worked to perfection, allowing the team to remove the foam pads from the folding cartons, the corrugate spacers from the shipper box, and reduce the overall length of folding cartons and shipper box. Needless to say that we passed ASTM D4169 with flying colors, including package integrity testing and product functionality.
In addition to the packaging system redesign, Pucará Engineering completed a revalidation of the large footprint FFS machine with he new forming and sealing dies, and optimized forming, sealing and printing parameters obtaining a machine efficiency above 95%.
Overall, we reduced the weight of the shipper box by 1.10 Lbs., which translated to over 300,000 Lbs./year of corrugate cardboard and foam removed from the waste stream, and a final cost savings in packaging material above $1MM/year.
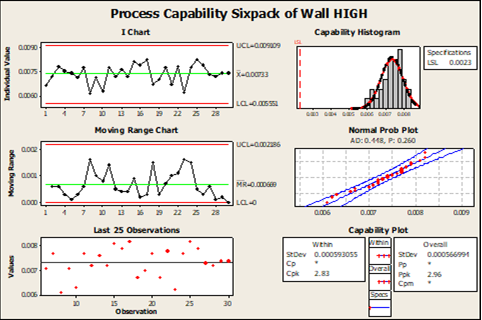
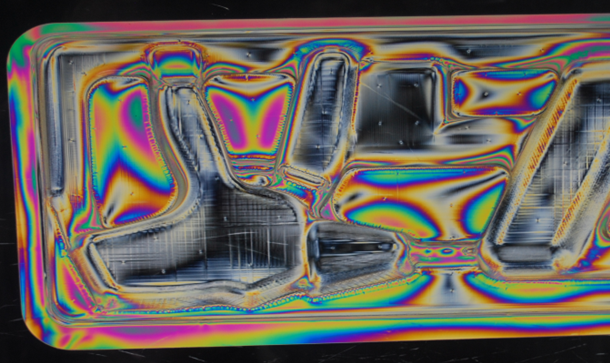
VALIDATION OF NEW MATERIAL REPLACING TYVEK®
A large medical device manufacturer established the goal to identify and validate a new material to replace 1073B Tyvek® used as lidding for flexible thermoformed blisters. We were tasked with testing a large number of prototype materials on a number of high-volume Form-Film and Seal machines, and make a recommendation on the materials selected for further testing. Prototype materials were tested for sealing, flexographic and thermal transfer printing properties, as well as human factors. Once the final material was selected, were completed a full process qualification of the new material on a number of high-volume FFS machines, and supported the customer’s packaging engineering team with packaging design verification and validations. Upon completion of this project, our customer had four of its largest volume FFS machines converted to the new material, achieved cost savings above $2MM/yearly, and protected the high-volume products from supply chain disruptions related to TYVEK®.
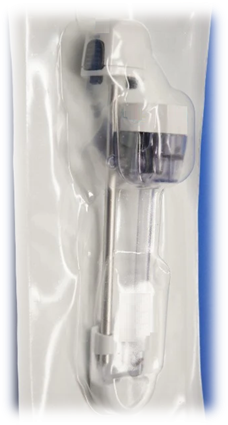